Quality Testing for Retail Security Solutions
Quality testing is a critical aspect of ensuring that all retail security products—from CCTV cameras and EAS systems to RFID tags—meet the highest standards of performance, durability, and reliability. Whether you’re purchasing pre-designed solutions through OEM or developing custom solutions through ODM, rigorous quality testing ensures that your security systems provide optimal protection for your store, inventory, and customers.
We take great pride in offering a comprehensive quality testing process for all our products, ensuring that every security solution meets or exceeds industry standards.
Our Quality Testing Process
1. Material and Component Inspection
Before manufacturing or assembly, we thoroughly inspect all raw materials and components used in our security systems. This includes:
- PCB boards for CCTV and EAS systems
- Sensors and RFID tags
- Wiring, cables, and other electrical components
Testing Includes:
- Visual Inspection for defects
- Electrical Testing to ensure components meet voltage and current specifications
- Material Testing to verify that plastics, metals, and other materials are durable and functional under varying conditions
Benefits:
- Ensures all materials used in the production of security systems meet durability and performance requirements.
- Reduces the risk of failures or product malfunctions during later stages of the manufacturing process.
2. Functional Testing
Once the components are assembled into a finished product, we conduct a series of functional tests to verify that the security systems perform as intended.
- CCTV Cameras: We test image resolution, field of view, night vision, and motion detection capabilities.
- EAS Systems: We test the alarm sensitivity, tag detection, and signal transmission for proper function in real-world environments.
- RFID Systems: We test the read range, accuracy of tracking, and integration with store management systems.
Testing Includes:
- Functional Simulation to replicate actual use conditions
- Stress Tests to evaluate performance under high usage, extended periods of operation, or extreme conditions
Benefits:
- Ensures that products meet performance expectations in real-world conditions.
- Identifies potential issues early on in the production process.
3. Environmental Testing
Security systems must be able to withstand a variety of environmental conditions, especially in retail stores where temperature, humidity, dust, and lighting can vary.
- Temperature Tests: Ensuring that products can operate in a wide range of temperatures (hot or cold).
- Humidity & Moisture Resistance: Testing for water resistance or moisture exposure in high-humidity environments (e.g., grocery stores or outdoor environments).
- Dust & Particle Testing: Ensuring the product can function in dusty or dirty environments.
Testing Includes:
- Heat and Cold Stress Tests: Devices are exposed to high and low temperatures for prolonged periods.
- Humidity Chamber Testing: Products are tested under controlled humidity levels to check for moisture-induced failures.
- Ingress Protection (IP) Rating: Testing products for their ability to resist dust, dirt, and water intrusion.
Benefits:
- Ensures that the product is durable and reliable, even in challenging environments.
- Meets IP ratings (such as IP65, IP67) required for devices exposed to outdoor or harsh conditions.
4. Durability & Stress Testing
Retail security products are used constantly, and they need to be durable enough to handle daily wear and tear. We conduct a variety of tests to simulate real-life use and stress conditions:
- Drop Tests: Dropping products from certain heights to simulate accidental falls.
- Vibration Tests: Subjecting products to vibration or movement to simulate transport or high-traffic store environments.
- Button Press Durability: For products with buttons or switches, we test the lifespan of buttons to ensure they won’t fail after extensive use.
Testing Includes:
- Drop Tests: Dropping devices from various heights to evaluate impact resistance.
- Vibration and Shock Tests: Devices are placed on a vibration table to simulate transport conditions.
- Cycle Testing: Frequently pressing buttons or switches for extended periods to ensure they continue to function without wear.
Benefits:
- Verifies the product’s ability to endure wear and tear over time.
- Reduces the likelihood of malfunctions due to mechanical issues or physical damage.
5. Software & Firmware Testing
For products that rely on software or firmware, such as smart cameras, RFID systems, and EAS software for monitoring, we ensure that the software is fully functional and bug-free.
- Security Camera Software: We test the user interface (UI) for ease of use, functionality, and integration with other systems (e.g., cloud storage or analytics tools).
- RFID Tagging Systems: Testing the compatibility of software with POS systems and inventory management platforms.
- Data Security: Ensuring that all communication between devices (e.g., alarms, cameras, or tags) is encrypted and secure.
Testing Includes:
- Firmware Functionality: Testing all features of the firmware, including remote access, motion detection, and alarms.
- Integration Testing: Verifying that the software integrates smoothly with other store systems, such as point-of-sale (POS) or security management platforms.
- Data Security & Privacy Testing: Ensuring all stored or transmitted data is secure and complies with privacy regulations.
Benefits:
- Guarantees that security systems are user-friendly and easy to integrate with your store’s existing infrastructure.
- Ensures that the software remains secure and functions correctly under various conditions.
6. Compliance and Certification Testing
To ensure that our products meet international industry standards, we conduct a final round of certification and compliance testing for the products.
- CE Certification: Ensuring that the product complies with European Union (EU) regulations for safety, health, and environmental protection.
- FCC Certification: For devices emitting radio frequency, we ensure that products meet Federal Communications Commission (FCC) standards in the U.S.
- RoHS Compliance: Ensuring that products are free from hazardous materials, in line with Restriction of Hazardous Substances (RoHS) regulations.
Benefits:
- Products are guaranteed to meet regulatory standards, ensuring safety and performance.
- Compliance with international regulations allows you to sell in global markets.
Conclusion
With our comprehensive quality testing process, you can be assured that our retail security solutions are not only effective but also durable, reliable, and ready for any challenges your store faces. From functional testing to environmental resistance and regulatory compliance, we ensure that every product meets the highest industry standards, so you can provide the best security for your store and customers.
Why Our Quality Testing Matters?
Reliability
We ensure that our retail security products will perform consistently and reliably, reducing the risk of system failure during critical moments.
Customer Satisfaction
Thorough testing guarantees that the end user—whether a store owner or customer—has a seamless experience with the security systems.
Reduced Downtime
Our rigorous testing process helps ensure that your security systems will not face unexpected malfunctions, leading to less downtime and better protection.
Regulatory Compliance
With certifications and compliance checks, we ensure that our products adhere to safety and legal standards, allowing you to operate without concerns about legal implications.
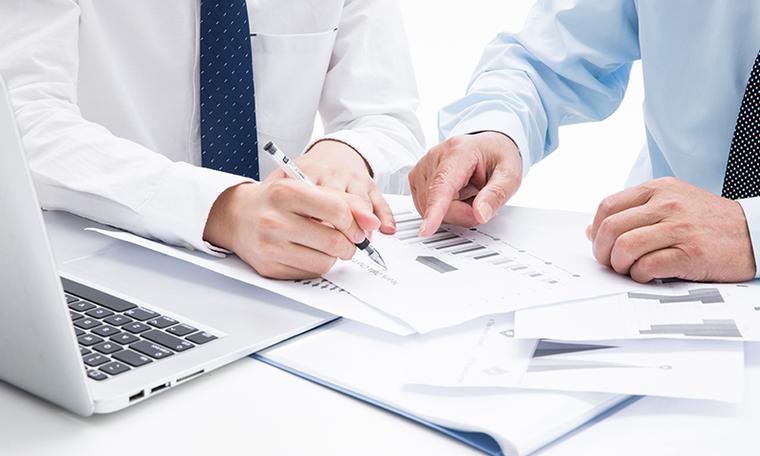
Contact us now!
Tel/WhatsApp:
E-mail:
Location: